在電子器件外殼中, 由于聯(lián)接(扣接)的需要, 很多壓鑄鎂合金或塑料件都有局部凸臺或薄筋, 或圓柱螺釘孔。 這在壓鑄和注塑成型工藝中是很容易實現(xiàn)的, 但對于沖壓工藝來說則是較難的。 過去國內(nèi)在隨身聽、MD 外殼上使用沖壓件時都是采用板件局部豁口, 結合彈簧實現(xiàn)的。沖壓成形的MD 鎂合金薄板件, 加工了局部豁口。 而用凸臺形式還沒有先例。近年來日本和中國臺灣的學者都在開展板件局部熱沖壓成形技術的研究, 目的是想以熱沖壓技術實現(xiàn)板材局部凸臺的成形, 這樣
鎂合金沖壓件就可以完全取代鎂合金壓鑄技術和塑料注塑技術了。 但這方面國內(nèi)外都很少有公開報道。
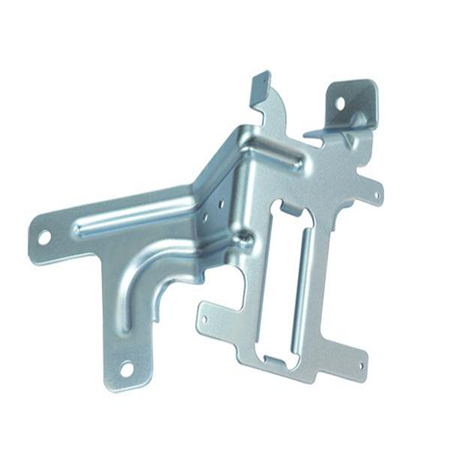
鎂合金板材局部沖壓成形時, 成形溫度要高一些, 最好在250℃以上, 以降低設備噸位。 另外, 潤滑技術是實現(xiàn)鎂合金薄板局部熱沖壓成形的關鍵, 一般凹模與坯料之間要采用合理的潤滑方式, 使坯料能夠合理流動。 凸臺金屬是由板材底部流入生成的, 板材一般產(chǎn)生明顯的減薄。 凸模速度也是影響材料成形流動的重要因素。 局部沖壓成形容易產(chǎn)生兩種工藝缺陷, 一種是板件凸臺背部的吸孔, 由凸臺增長過快而材料流動補充不足造成的。 另一種是凸臺根部薄弱, 卸料時折斷。 在底部變薄到一定程度時, 如果凸臺已經(jīng)充滿, 繼續(xù)加大底部變形就會在凸臺根部產(chǎn)生金屬“ 穿流”, 即在繼續(xù)變形時材料垂直于已經(jīng)成形的凸臺流動。 橫向剪切變形破壞已有的金屬流線, 強度較弱, 變形量增大時發(fā)生折斷。 為防止這種缺陷, 可減小坯料厚度或者提高凸臺成形阻力來達到一致變形, 形成有益的金屬流線。